Call Us 281-940-KELM
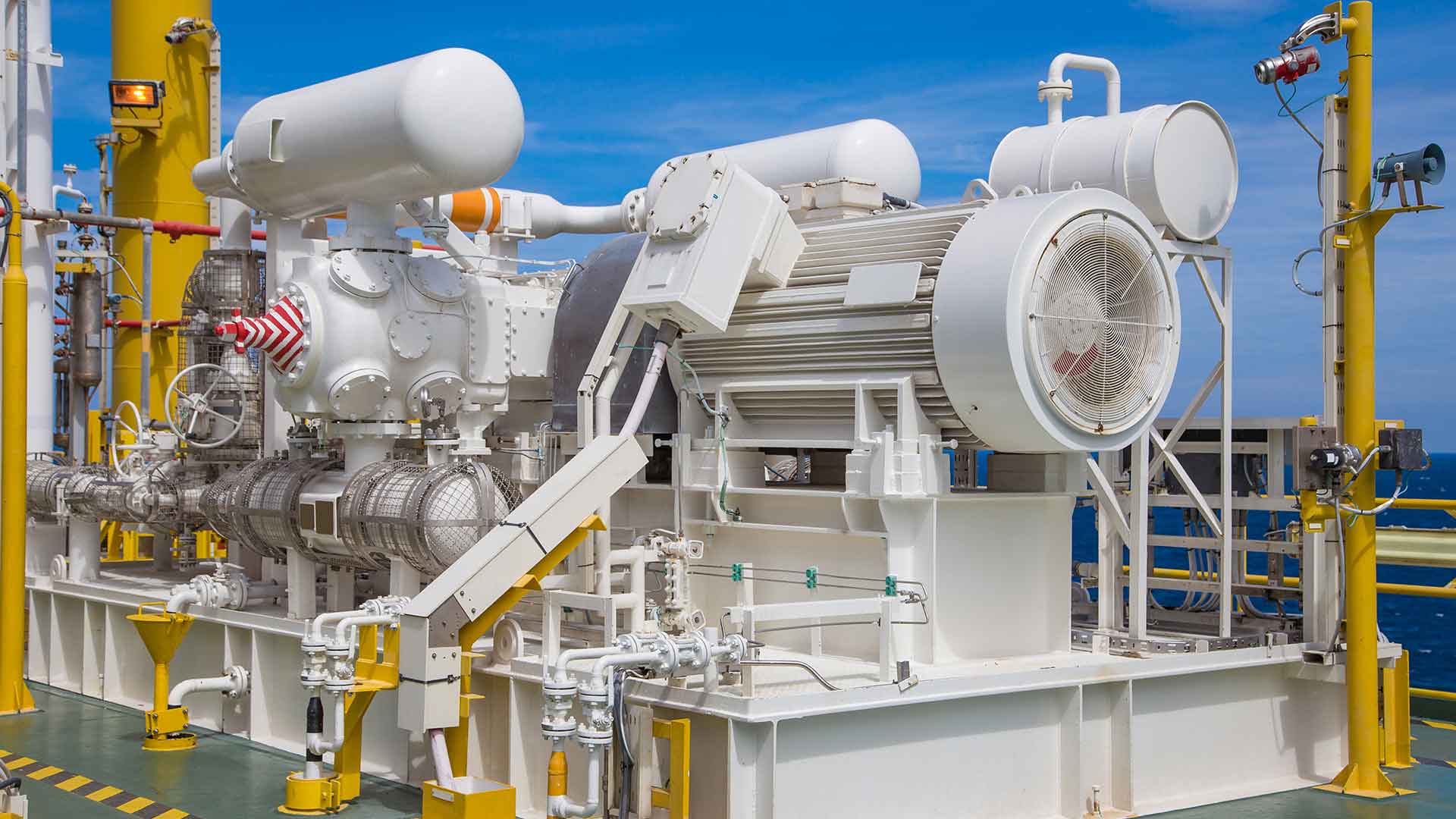
FINITE ELEMENT ANALYSIS
Finite Element Analysis Finite element analysis (FEA) is a modeling tool used to accurately calculate stresses, deflection, natural frequencies and dynamic responses of mechanical systems. We use ANSYS modeling software and commonly model a variety of systems and individual components. FEA can be used on individual components or on large systems depending on the purpose for the required analysis. ANSYS is a general finite element modeling tool that has a huge variety of element types including solid modeling, non-linear contact, beams and shells, springs/dampers, lumped mass, and a wide range of others. We have modeled numerous systems, including crankshafts, turbine blades, compressor impellers, fan wheels, coupling components, concrete and steel structures supporting machinery, piping systems, pressure vessels, and valve components. Some models require non-linear materials models to address material yielding, creep, or local yielding. Many non-linear effects can also be modeled including contact between components as with bolts/washers bearing against parts, or interference fits between a hub or disk and a shaft.
Benefits of Finite Element Analysis
FEA can provide very accurate answers to difficult problems due to the ability to model very complicated geometries. Alternatives to FEA include hand calculations or extensive testing of components. Due to the capability of the software, the stress results are much more accurate than hand calculations since actual geometry induced stress concentrations are directly calculated. This makes the stress amplitudes approach true values with proper modeling techniques. Component testing can be very expensive and can produce mixed results unless many components are tested to verify the results. Many of the models we generate are used to assist in other analysis or diagnostic activities to support problem solving or equipment troubleshooting. Anyone with basic training can run FEA software, but generating models and calculating results that result in practical solutions to real problems require specially trained and capable engineers.
Our Approach to Finite Element Analysis
Most models are generated using the ANSYS modeling capabilities. We also have the capability to import various CAD geometries from a number of modeling tools. Once the models are generated, models are meshed and loaded. Once the proper loading is applied, the results are reviewed for accuracy. Mesh studies are commonly done to verify the numerical results vs element size to improve the accuracy of the results. We have the computing capability to develop and analyze very large models using a variety of multiple core computers with large amounts of RAM and high speed hard drives.
Kelm for Finite Element Analysis
At Kelm, we recommend that you have your system or systems checked for deflections, stresses, and frequencies to make certain everything is in proper working order. Find out how your systems are running through Kelm’s finite element analysis.