Call Us 281-940-KELM
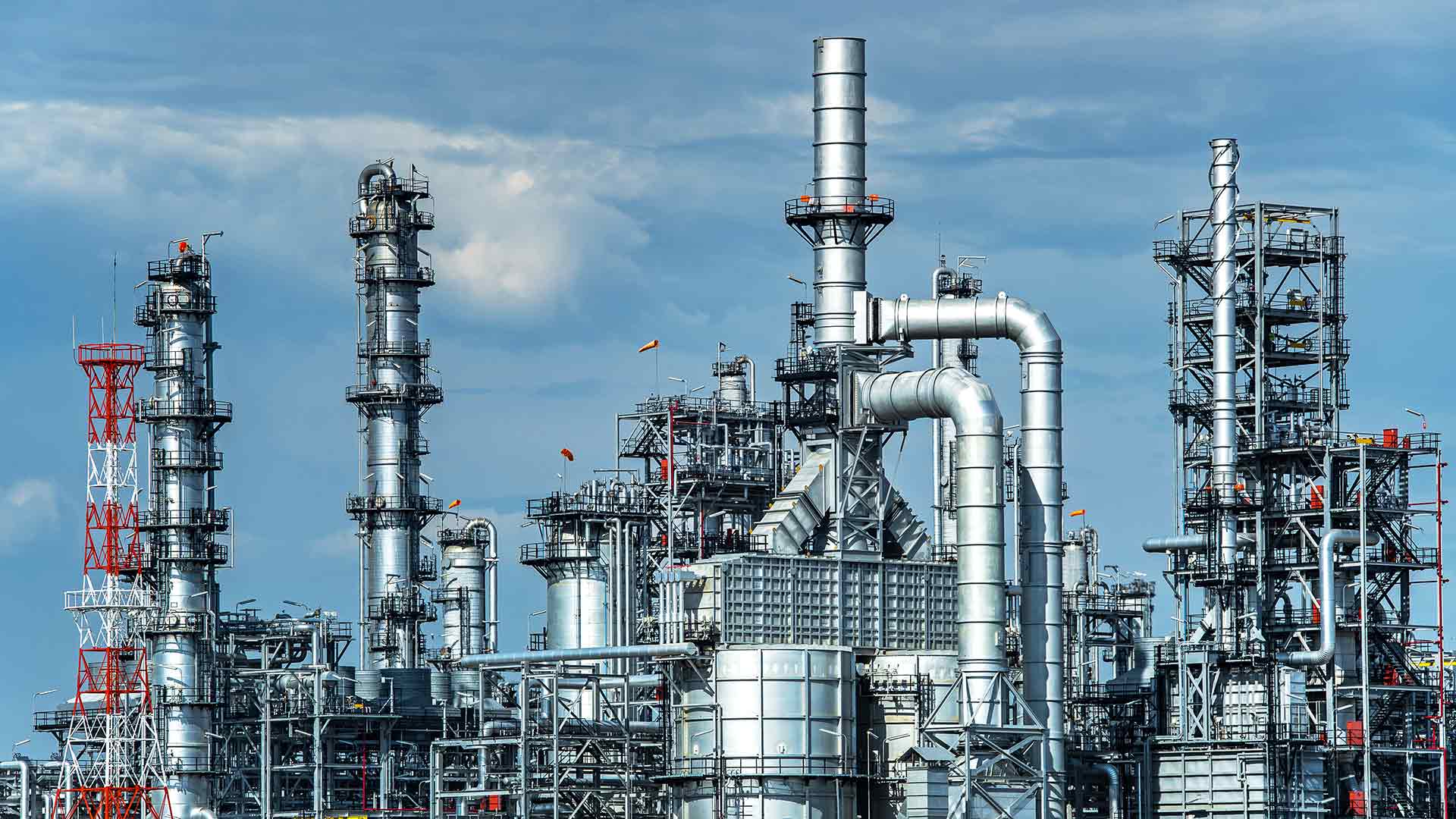
PIPING FATIGUE ANALYSIS
Piping fatigue will occur in pipe systems when the combinations of static and dynamic stresses in the piping components exceed allowable values. Static stress in the pipe is most commonly caused by a combination of pressure and thermal growth. Thermal stress can be very large particularly if supports are not installed or maintained properly. Dynamic stress can result from vibration transmitted by connected machinery, forces generated inside the pipe from water hammer or pressure pulsations, or by fluid induced or other external loads.
Pipe Fatigue Failures
When a pipe has a fatigue failure, there is usually release of containment of the process fluid. This can result in dangerous release of flammable or lethal products, or may put personnel at risk from high pressure/temperature steam or other fluids. Failure can occur very quickly in some cases, or may arise after long run times due to an accumulation of dynamic stress cycles. A machine operating at 3,600 RPM will normally experience a fatigue failure in 10 hours or less when the stresses exceed allowable values for high cycle fatigue due to high machine induced vibration. Thermal stress cycles (heating and cooling cycles of the piping system) can result in a fatigue failure after many years due to the low number of cycles but with higher amplitudes.
Benefits of Conducting Piping Fatigue Analysis
When failures occur in piping systems, the safety and environmental risks to personnel and property with often warrant evaluation of the failure to identify corrective actions to prevent re-occurrence. Proper analyses of the failed components as well as applied loading are used to identify the cause for failure. Once the cause of failure is known, appropriate solutions are identified to eliminate the causes are to greatly reduce the risk of future failures.
How Kelm Conducts Piping Fatigue Analysis
Piping fatigue is evaluated using multiple approaches often at the same time. Initially, inspection and possible metallurgical analysis of the fracture surfaces are used to identify if the fracture has evidence of fatigue. If so, stress analysis is performed using either ANSYS finite element analysis software or AutoPipe pipe modeling software. In some situations it is necessary to measure actual stresses, loads or vibration response of the piping system. We have a variety of field test and measurement tools that we use for documentation and verification of loads and stresses. Once solutions are identified, we will often perform field testing to verify whether the solution is effective at eliminating the risk for a future failure due to the same causes.